The Company
Celina Aluminum Precision Technology Inc.–otherwise known as CAPT for short–was established in Celina, OH in 1994. Our associates and their families live in Celina and the nearby communities. CAPT’s commitment to these communities is to demonstrate appreciation through service and support and to ensure our manufacturing operations do not negatively impact our neighbors.
The Celina-Mercer County area provides CAPT with associates dedicated to producing quality products. Our location in Northwest Ohio and proximity to a developed transportation network assure timely delivery of those products. As a growing member of the community, CAPT is proud to support the area through volunteer activities, local athletic programs and special events.
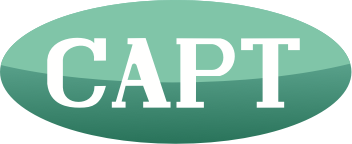
Our Values
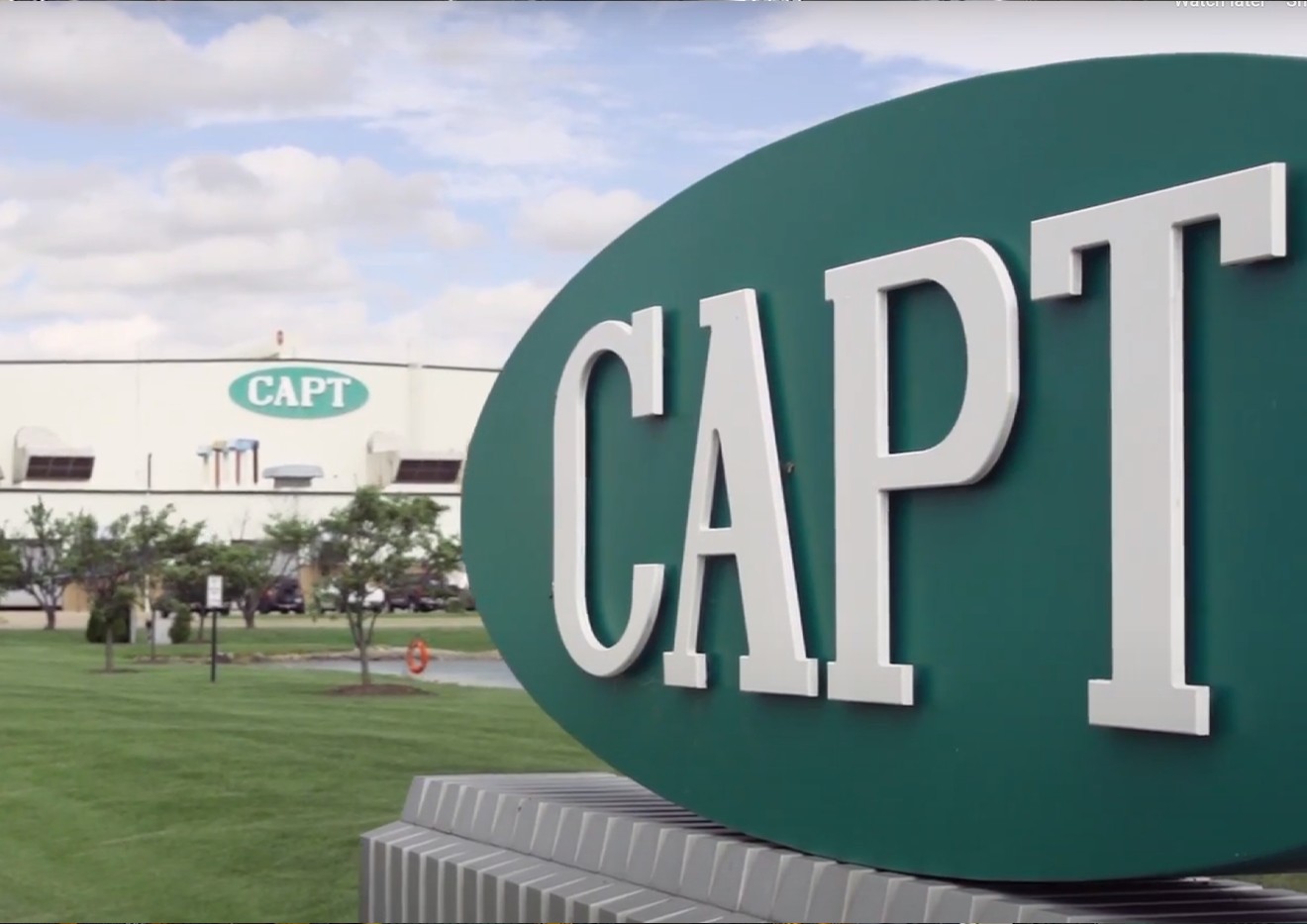
With our worldwide viewpoint, we always supply highest quality and reasonable priced products with our excellent technology.
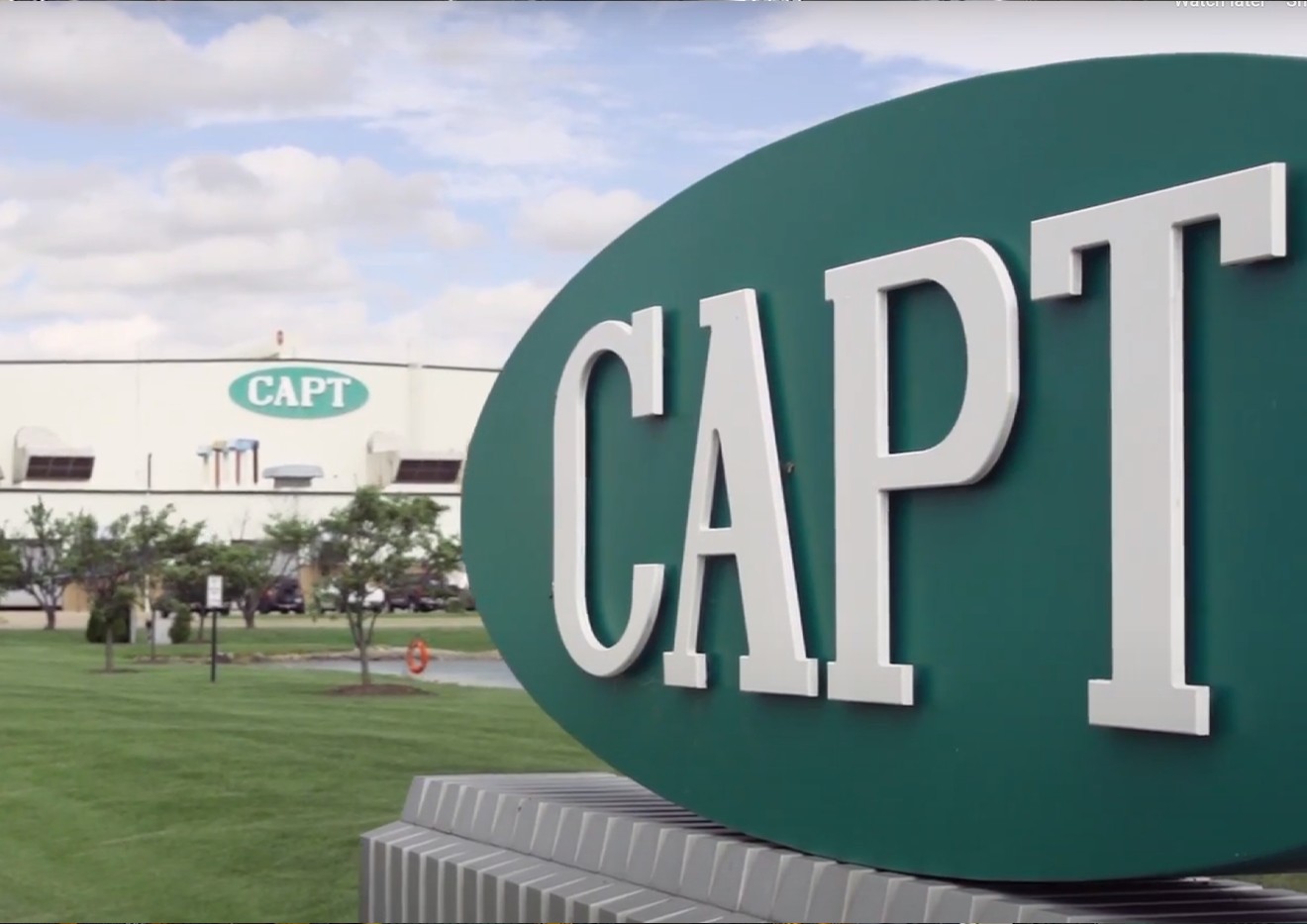
CAPT associates, working together to produce the highest quality product at a reasonable cost, while maintaining global customer satisfaction, compliance to all regulatory requirements and striving for continual improvement.
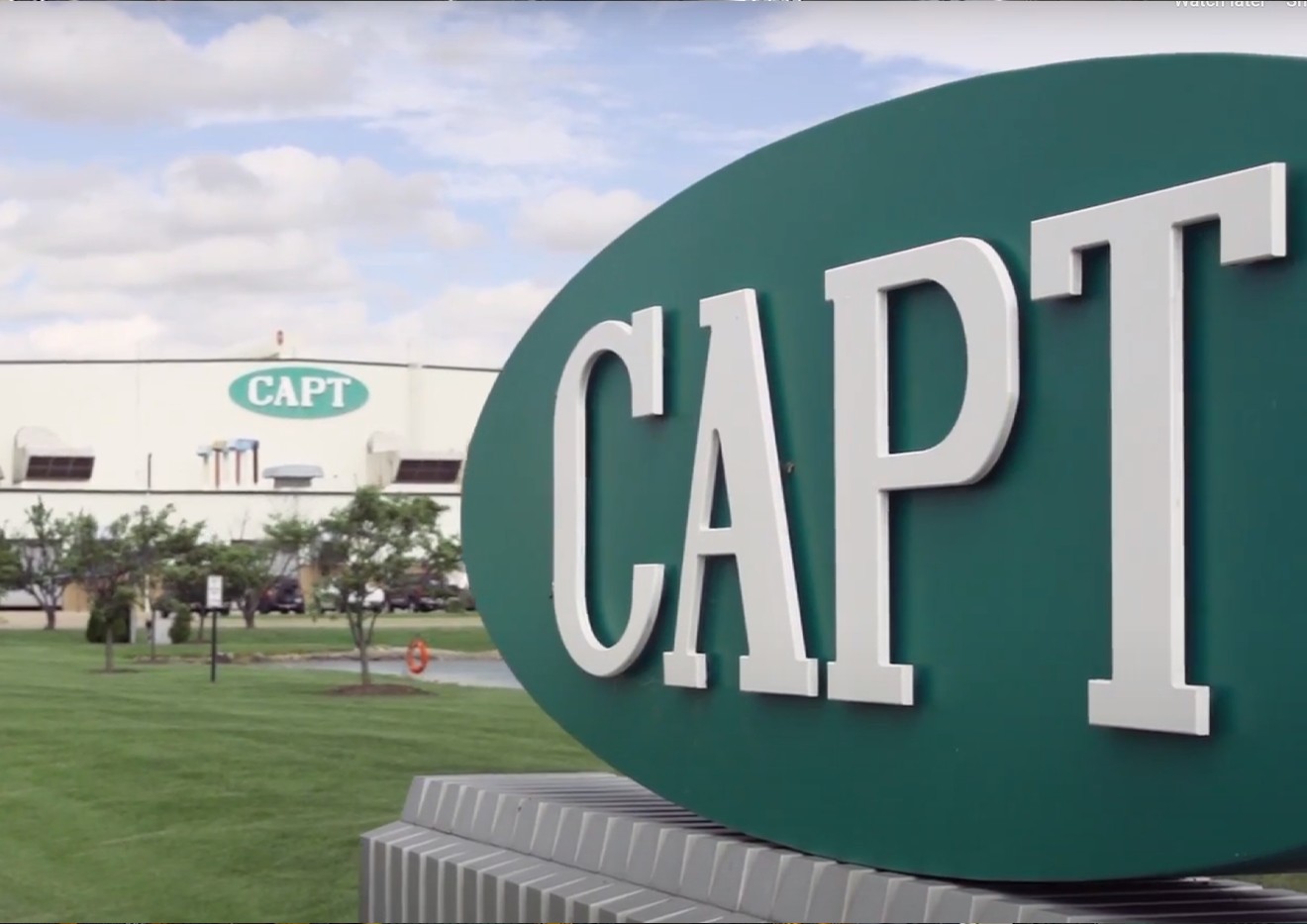
The successful business operation and reputation of CAPT is built upon the principles of fair dealing and ethical conduct for our associates. Our reputation for integrity and excellence requires careful observance of the spirit and letter of all applicable laws and regulations, as well as regard for the highest standards of conduct and personal integrity.
The continued success of CAPT is dependent upon our customer’s trust and we are dedicated to preserving that trust. Associates owe a duty to CAPT, our customers, and shareholders to act in a way that will merit the continued trust and confidence of the public.
CAPT complies with all applicable laws and regulations and expects its directors, officers, and associates to conduct business in accordance with the letter, spirit, and intent of these relevant laws and regulations by refraining from any illegal, dishonest, or unethical conduct.
CAPT uses NAVEX Global for Ethics and Compliance. The phone number is 844-502-7950 or you can visit their website here.
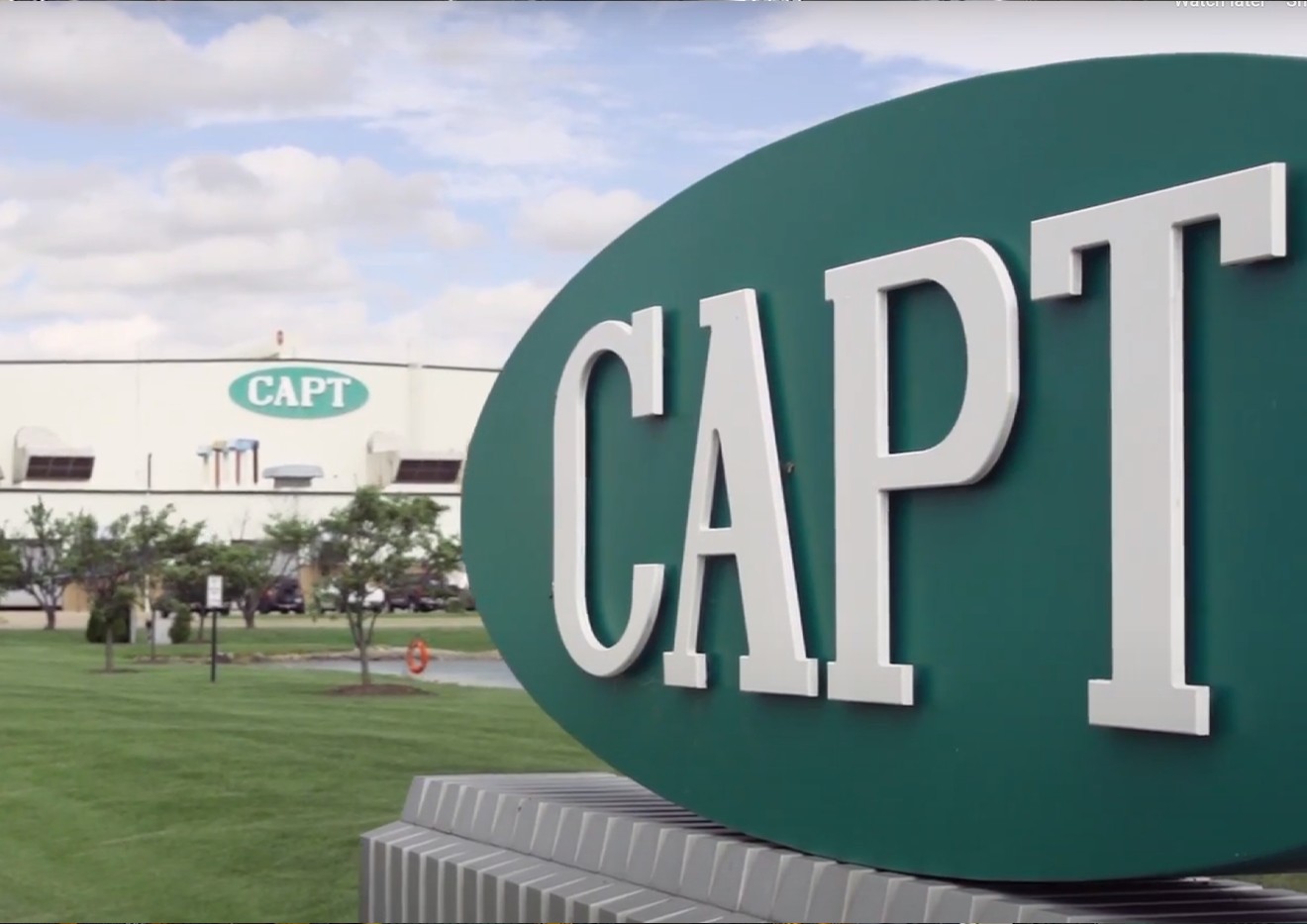
As an environmentally responsible neighbor, CAPT is committed to:
- Prevention of pollution
- Compliance with legal & other environmental requirements
- Continual improvement of our environmental management system
Production Process
At first glance, one might not fully appreciate the significance of CAPT’s products. By mastering the art of melting, casting and machining aluminum, CAPT’s manufacturing processes result in the highest quality aluminum products. These products become part of legendary Honda automobile engines – engines known for efficient operation, reduced friction, higher output and enhanced gas mileage.
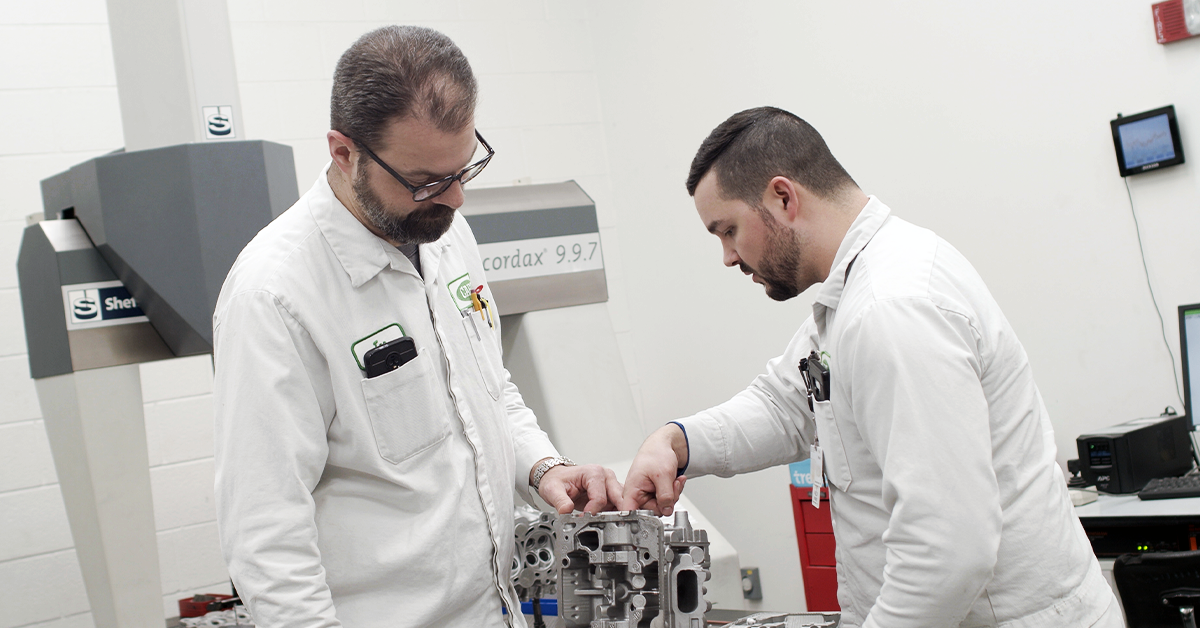
Parts We Manufacture
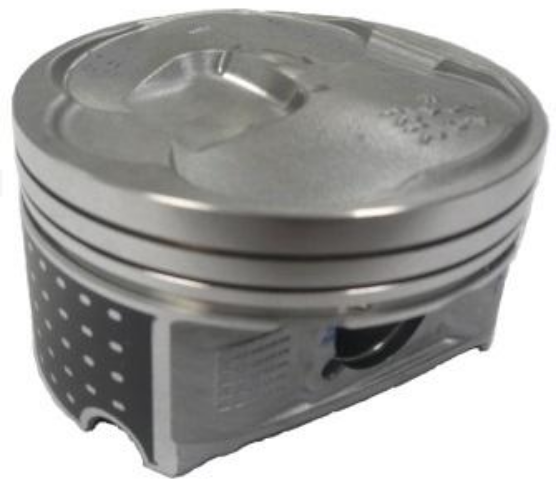
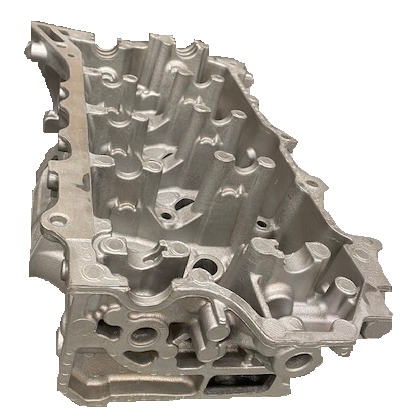
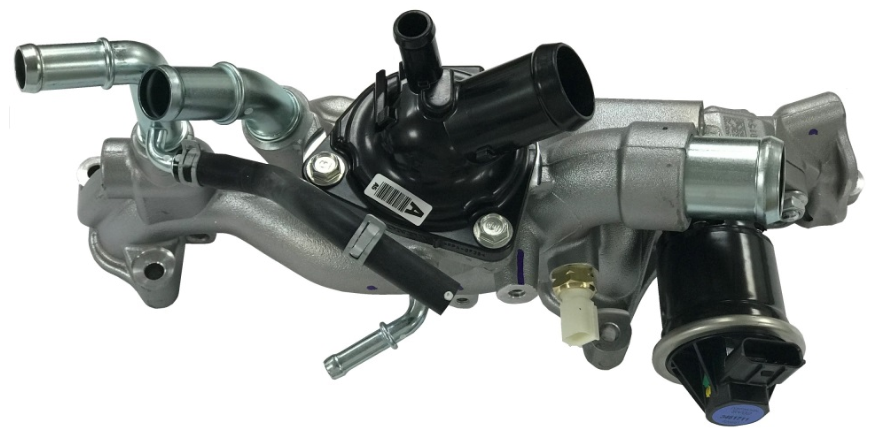
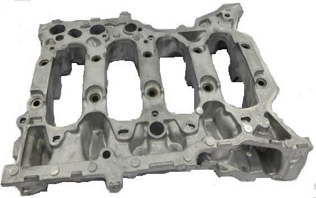
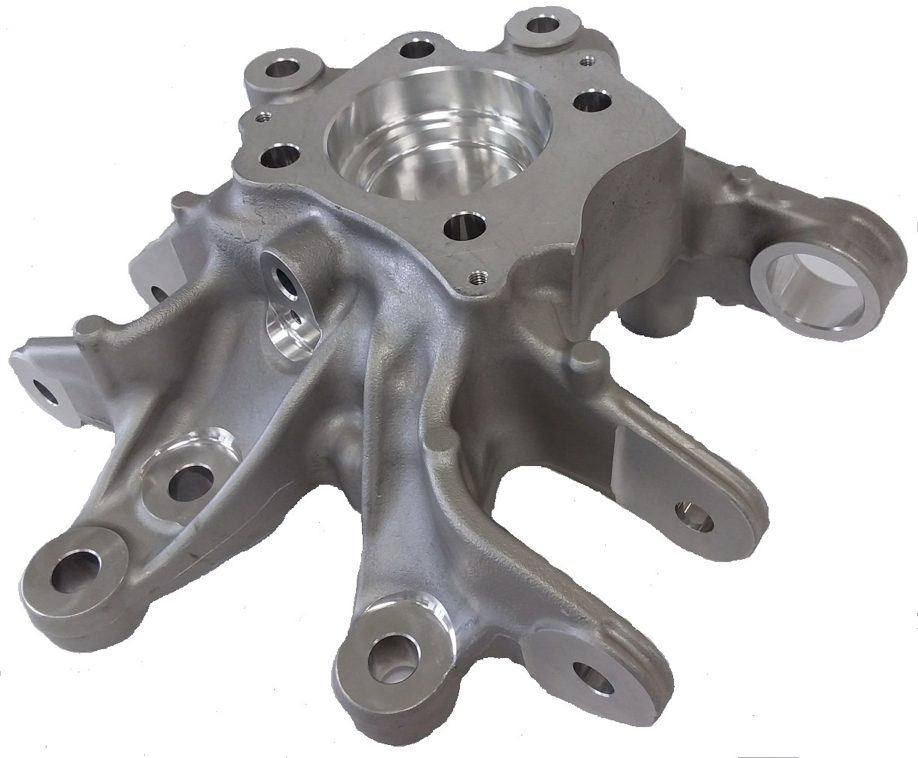
Piston
- Mass Produced since January 1996
- Casting Method: Gravity
- Machining
- Surface Treatment
Cylinder Head
- Mass Produced since August 1996
- Casting Method: Low Pressure
Water Passage
- Mass Produced since July 1998
- Casting Method: Tilt Gravity
- Machining
- Assembly
Lower Block
- Mass Produced since August 2005
- Casting Method: High Pressure
- Machining
- Assembly
Knuckle
- Mass Produced since August 2006
- Casting Method: Tilt Gravity
- Machining
- Assembly